

At the core of our business is screen printing. We’re the first company to develop and implement UV LED ink curing technology for screen printing in our industry. We build sustainability directly into our manufacturing process. As we continue to push technology, we’ve expanded our capabilities to manufacture with both sheet-fed and roll-to-roll printing presses.
Empire Screen Printing President John Freismuth wrote an article about how we're making a more environmentally-friendly way to screen print .
Screen printing is the oldest form of printing, dating back to China during the Song Dynasty (960-1279 AD). The longevity of screen printing remains due to the wide variety of materials, inks, durability, and specialized properties other printing methods can't replicate.
More details about screen printing (PDF)
Screen printing uses an oversized stencil to print images onto material (substrate). We first stretch fabric (mesh) across a metal frame, making a screen. The screen is then coated with emulsion.
Using a computer-imaging device, the screen is exposed to beams of light that transfers the image onto the mesh. When washed, the emulsion creates an impermeable barrier (stencil) within the mesh, filling the gaps and preventing ink from seeping through the negative spaces of the image, leaving the remaining areas open.
The screen is laid overtop the material, and ink is poured onto the screen. A flood bar spreads the ink evenly over the surface of the screen, and a squeegee pushes ink through the open areas, transferring the image onto the material below. For each color needed, this step is repeated with more screens. When all the colors are combined onto the material, it produces the final design.
The 12-color Legacy Press was built in-house by Empire employees to print more than six colors in one pass. With our exclusive registration system, the press holds mechanical tolerances of .001" and can hold color-to-color registration between .005" - .007". This greatly improves efficiency in quality and lead times for our customers, expanding our capacity by 25%.
ROLL-TO-ROLL SCREEN PRINTING
The Kammann K-61 EcoPress is the first screen press in the world to use a UV LED ink curing system, making it the most economically-sound and environmentally-friendly screen printing press on the market.
Using roll labels results in less material wasted, as the roll stock has a thinner liner than sheet stock and is less sensitive to dust and contamination. Other benefits include:
- Completion of parts from start to finish in a one-piece flow
- Reduced material waste
- Enhanced flexibility, precision, and quality
- Air-cooled LED UV-curing means less operating heat
- Decals can be supplied in rolls or as individual sheets
- Unlimited number of colors
- Reduced energy consumption
- No ozone emissions
More information about Empire's roll-to-roll capabilities (PDF)
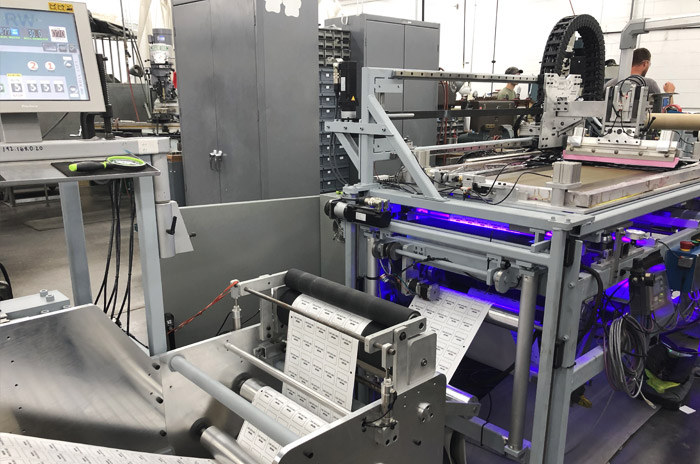
Introducing Empire's Roll-X, our large format, multi-color, roll-to-roll screening press. It combines a visual registered roll finishing line unlike any other. This press includes our own patent-pending registration platform, automated chase, vacuum functions, and a completely standardized set-up system which eliminates variability during machine operations. These advancements in registration allow the material to re-register to itself when needed.
This complete module unit is designed to add multiple inline print tables for maximum efficiency from start to finish. By reducing downtime, it increases efficiency and shortens lead times while creating a quality level our industry has never seen. Empire created this equipment with visual registration to ensure repeatability. This gives our customers peace of mind that their branding will remain consistent throughout their product cycle.

